A Škoda Fabia RS Rally2 versenyautó használatát a versenyeken az autó megépítéséhez szükséges egyes alkatrészek gyártási, logisztikai és összeszerelésének igényes és összetett folyamatai előzik meg. A Skoda Motorsport bemutatta ezeket a folyamatokat.
A folyamat leírását két részre bontva lehet bemutatni. Az első az első tengely. Ez rendkívül fontos alkatrész az autó általános tartóssága szempontjából, hiszen a kerékfelfüggesztés és a kormányzás ehhez kapcsolódik. Éppen ezért a tengelyt közvetlenül a Škoda Motorsport fejlesztőcsapata tervezte, a versenyautók futómű-fejlesztésében szerzett sokéves egyedülálló know-how alapján, és a gyártást gondosan felügyelik. A második rész a motorblokk. Bár ez az EA888 sorozatgyártású motorblokkon alapul, egy külső szállítónak módosítania kell, hogy megfeleljen a versenyautó igényeinek, mielőtt beszerelhető lesz. De először nézzük meg magát a gyártási folyamatot.
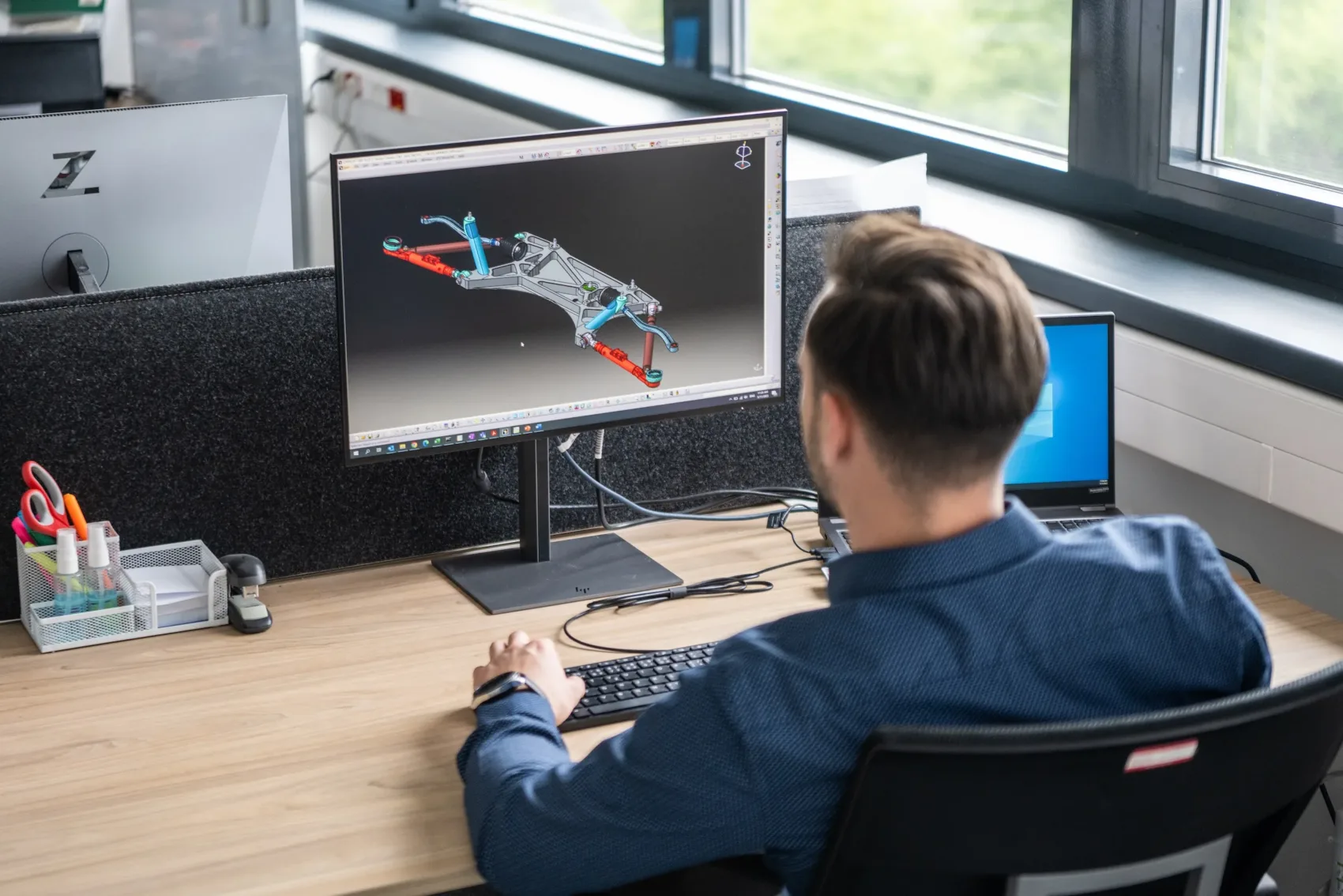
Gyártás a legmagasabb igényekkel
Az első tengelyek az alváz többi részéhez hasonlóan jelentősen eltérnek a sorozatgyártású autók alvázrészeitől. Biztonsági és megbízhatósági szempontból lényegesen nagyobb erőket, ütéseket és egyéb igénybevételeket kell elviselniük, amelyek a kerekekről a karokon keresztül jutnak át a karosszériába. Felépítésének és felületkezelésének biztosítania kell a megbízható működést száraz körülmények között, esőben, hóban, sárban és homokban. Meg kell felelnie az FIA szabályainak is, amelyek előírják a minimális tömegét, a maximális árát, de a kinematikus felfüggesztési pontok alaphelyzetét is. Természetesen kialakításának kulcsfontosságú paramétere a szervizszünet alatti könnyű csere is.
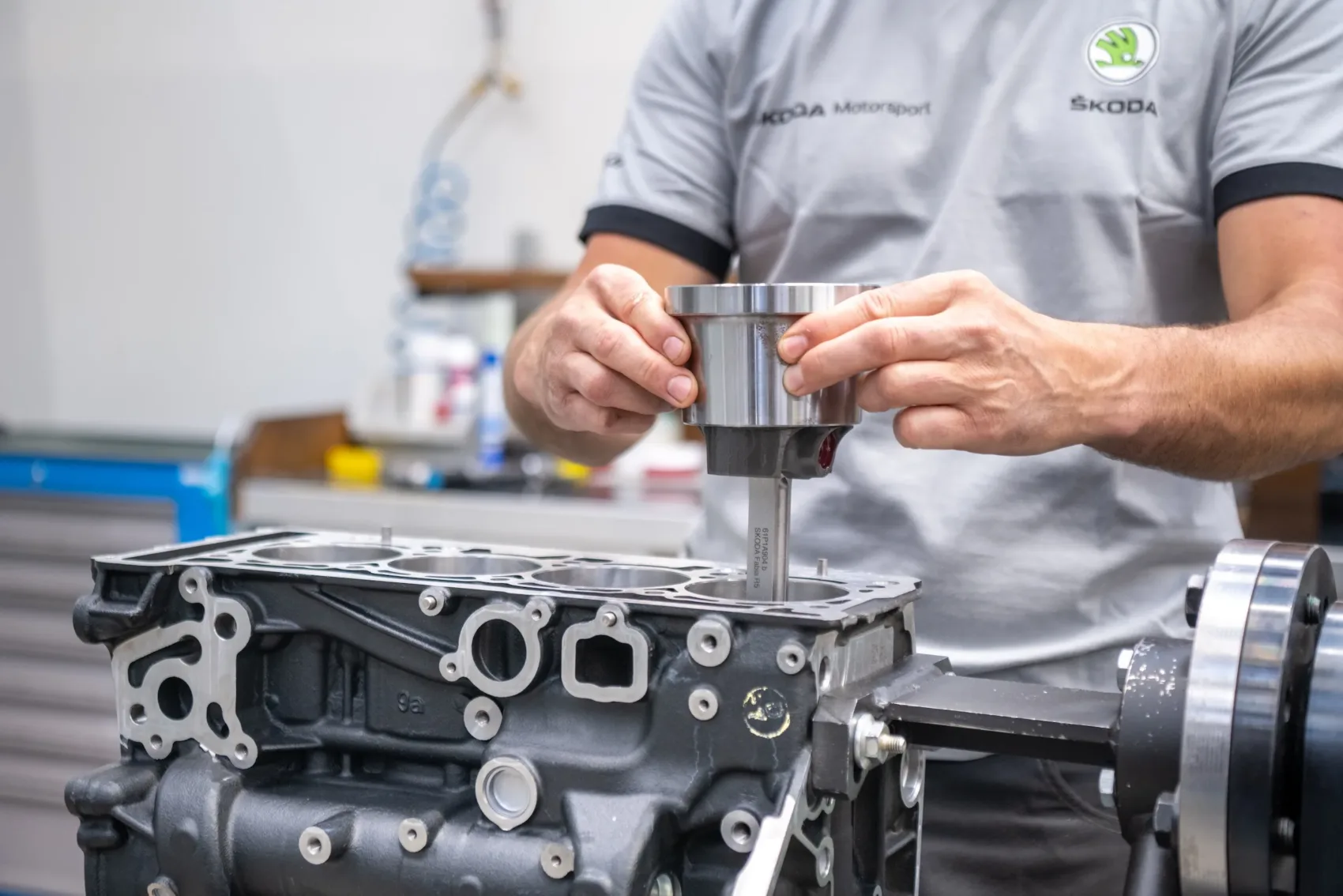
Az alkatrész összetettsége miatt az első tengelydoboz gyártása több szakaszból áll. Az egész folyamat az anyag előkészítésével kezdődik, ezt követi a legtöbb megmunkálási művelet és a csövek hegesztése a karosszériához való rögzítéshez. A következő szakaszban a tengelydobozt hőkezelésnek vetik alá, hogy biztosítsák az anyag szükséges szilárdsági tulajdonságait. Ezután már csak a felületkezelés és a végső megmunkálás van hátra. Az alkatrész teljes gyártása két hét alatt befejezhető.
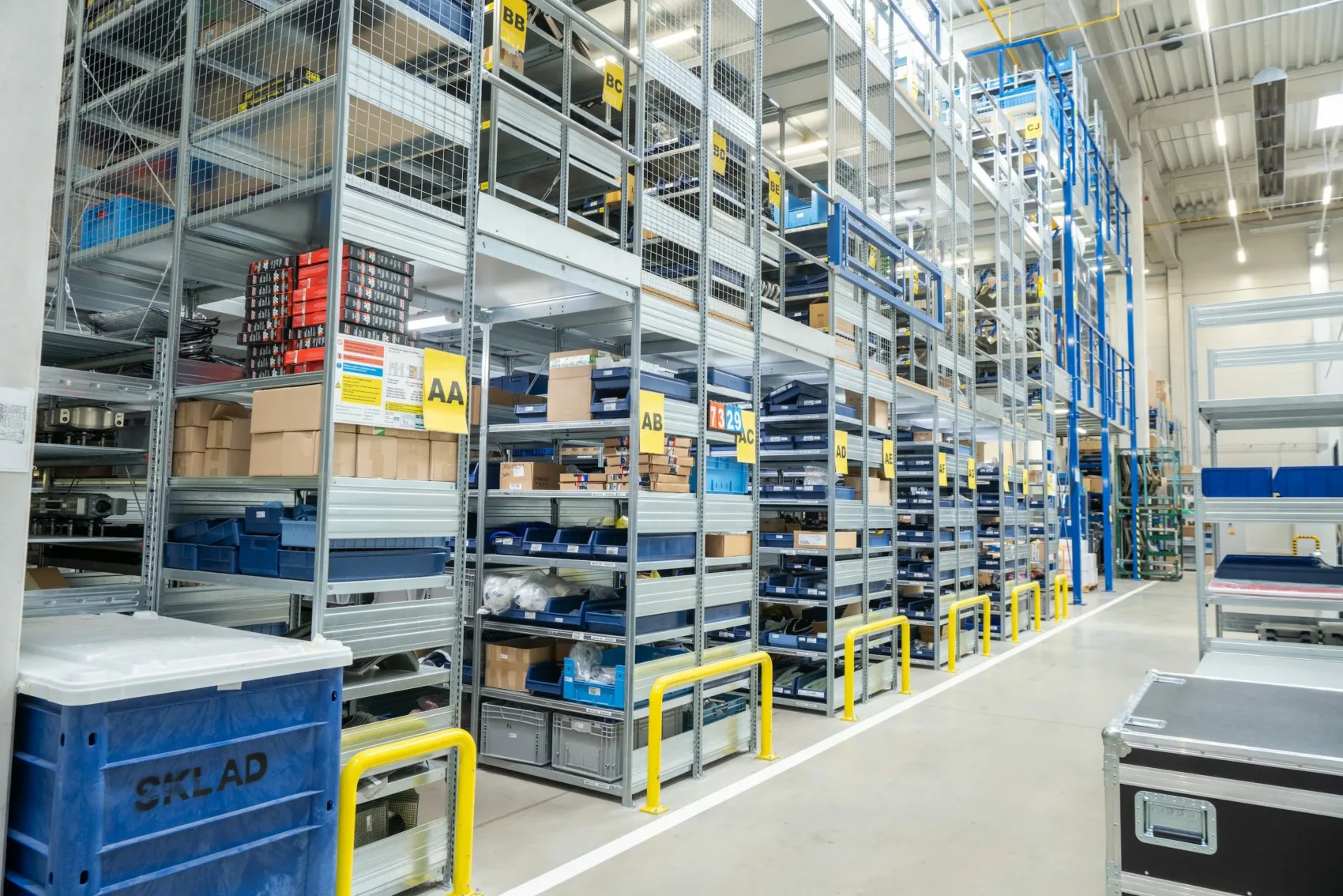
A motorblokk esetében a gyártási folyamat első pillantásra egyszerűbbnek tűnik. Alapként a sorozatgyártású motorblokkot használják, amely megtalálható például a Škoda Octavia 2.0 TSI-ben. Az FIA lehetővé teszi a dugattyúfuratok és a fő csapágyfedél megmunkálását egy további nyomócsapágypár felszereléséhez erre a blokkra. Versenyautókon való használatra a blokk kulcsfontosságú módosítása 1 mm-es furatnövelés. Ezután az újonnan fúrt hengerek falait újra kell burkolni. Az új furat kivitelezése a forma és a felület minősége szempontjából szó szerint alkímia. Ezt a folyamatot hónolásnak nevezik. A dugattyú mozgásához a henger alakjának a lehető leghengeresebbnek kell lennie. A fej tényleges rögzítése a blokkra akkora deformációt okoz, hogy az negatív hatással van a kívánt tömítettségre. Emiatt figyelembe kell venni a hengerfej merevségének a henger alakra gyakorolt hatását. A dugattyúrész megfelelő kenéséhez be kell állítani az előfeszítést és a hónolókövek mozgási szögét a hónológépen. Ez egy mérnöki know-how, mert ha nem megfelelően végzik, a motor magas olajfogyasztással működik, vagy gyorsan elhasználódik. Ezek a blokkbeállítások körülbelül 1 hónapot vesznek igénybe. A külső beszállítóktól mindkét alkatrész először a Škoda Motorsport raktárába kerül.
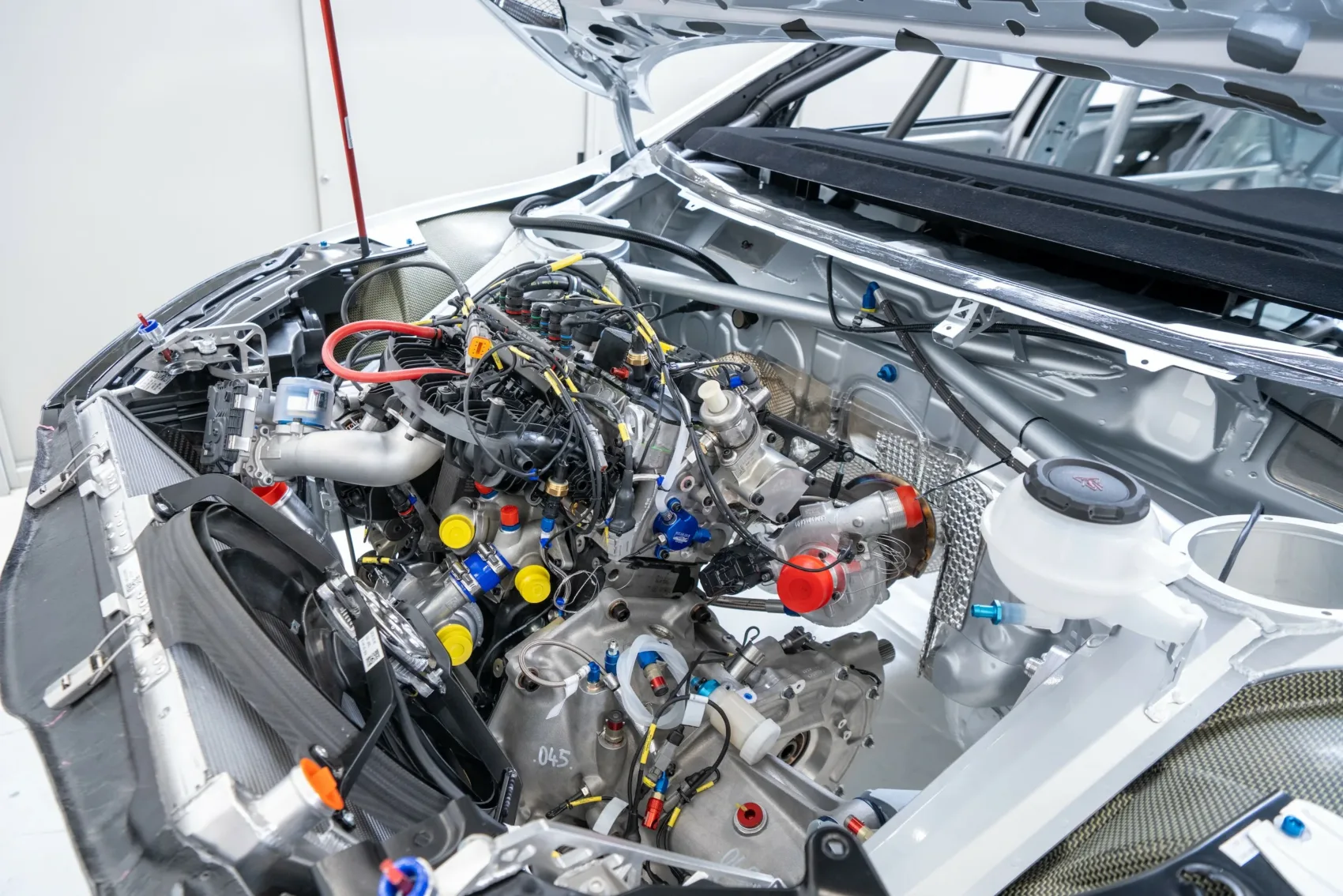
A logisztika kihívása
A raktár teljes területe több mint 2200 négyzetméter, amelynek több mint egyharmada közvetlenül a Škoda Motorsport telephelye, a többi pedig külső raktárterület Mladá Boleslavban. A raktárt 15 alkalmazott üzemelteti, a raktárban összesen 5500 féle alkatrész van a Fabia Rally2, Fabia Rally2 evo és Fabia RS Rally2 számára. Az alkatrészkészlet ellenőrzése azonban nem a raktár felelőssége. Ezt a selejtezési osztály ellenőrzi, amely igény szerint szállítói rendelések alapján tölti fel a készletet. A raktár az autók gyártásához szükséges alkatrészeket tárolja, de a vevőket is ellátja alkatrészekkel. A Škoda Motorsport 48 órán belül képes raktározni és kiszállítani az alkatrészeket.
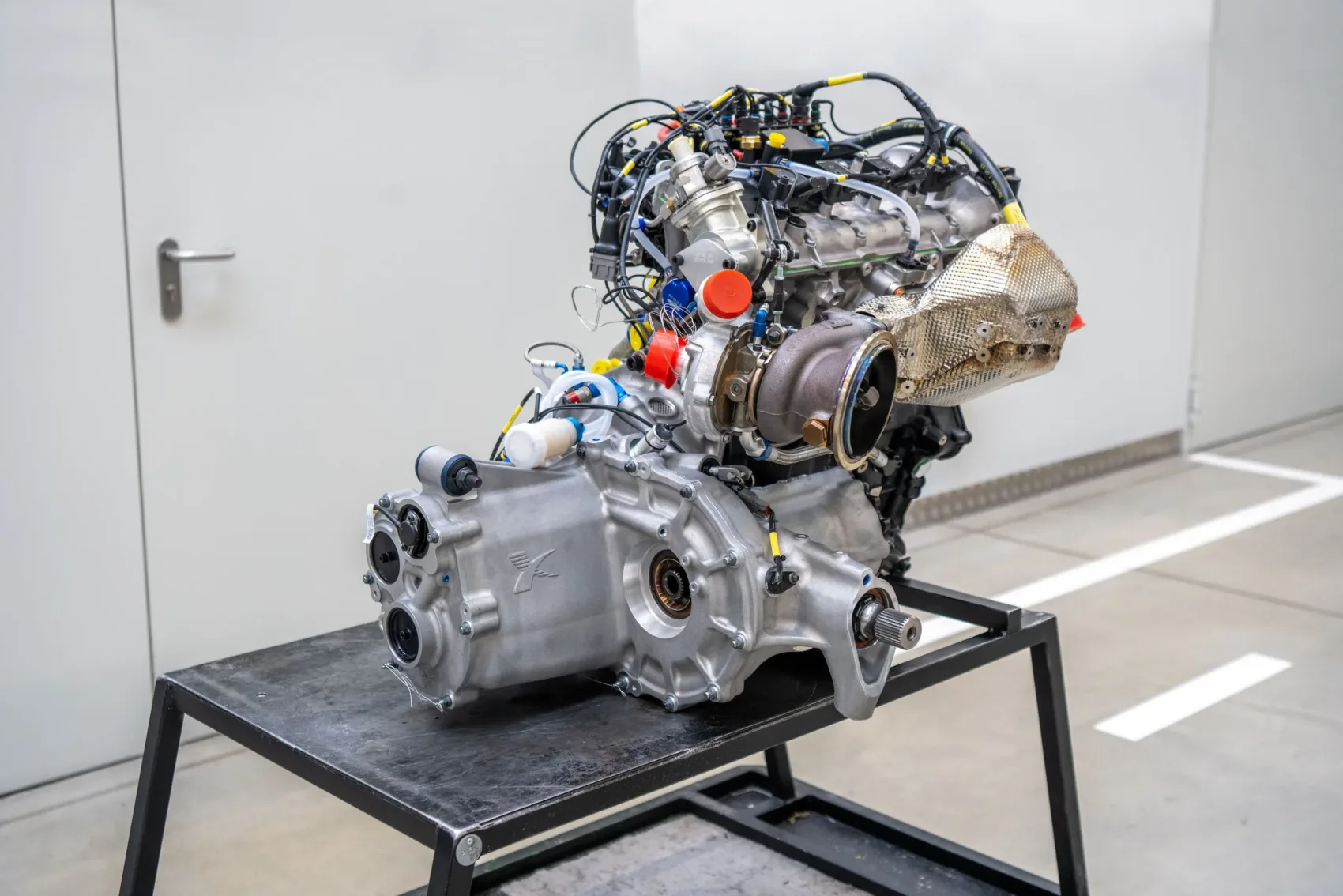
Az ügyfelek felé a logisztika szempontjából a legnagyobb kihívást mindenképpen a karosszéria jelenti. A kezeléséhez speciális raklapot kellett kifejleszteni. Festési igény esetén a csapatnak a karosszériát is el kell küldenie a festőműhelybe, mielőtt az ügyfélhez szállítaná. A szélvédők kezelése is meglehetősen összetett, speciális kezelést igényel a csomagolás és a szállítás során. A raktári kínálatban a legkeresettebb alkatrészek természetesen a fékelemek, lökhárítók, szűrők.
Alapos minőség-ellenőrzés
A tengely és a motorblokk esetében a minőség-ellenőrzés kulcsfontosságú része a rakodási folyamatnak. Alapos ellenőrzés és mérés nélkül az ilyen fontos alkatrészeket nem lehet raktárra venni.
A minőség-ellenőrző csapat az általánosan elérhető mérőeszközökön, például digitális tolómérőkön, digitális mikrométereken és mérlegeken kívül a Zeiss csoport által gyártott kifinomult 3D mérőműszerekkel is dolgozik. És ezeket a csúcstechnológiás műszereket motorblokkok és tengelyek mérésére is használják. Kifinomult optikai rendszereiket rendszeresen kalibrálják, hogy biztosítsák a maximális mérési pontosságot és ellenőrizzék, hogy a figyelt méretek a tervező által meghatározott tűréshatárokon belül vannak-e. Általánosságban elmondható, hogy minél magasabb a pontossági követelmény egy alkatrésznél, annál drágább a gyártása. Az így létrejövő gyártási tűrés tehát kompromisszumot jelent az alkatrész funkcionalitása és a gyártási költség között.
A tengelytartó alapméretein kívül a karok tengelydobozhoz való rögzítési pontjainak kialakítását is megmérik. Ezen úgynevezett kinematikai pontok egymáshoz viszonyított helyzetét és kialakítását kifinomult 3D mérőgépeken mérik. A homologizált tengelydoboz teljes tömegét is ellenőrzik.
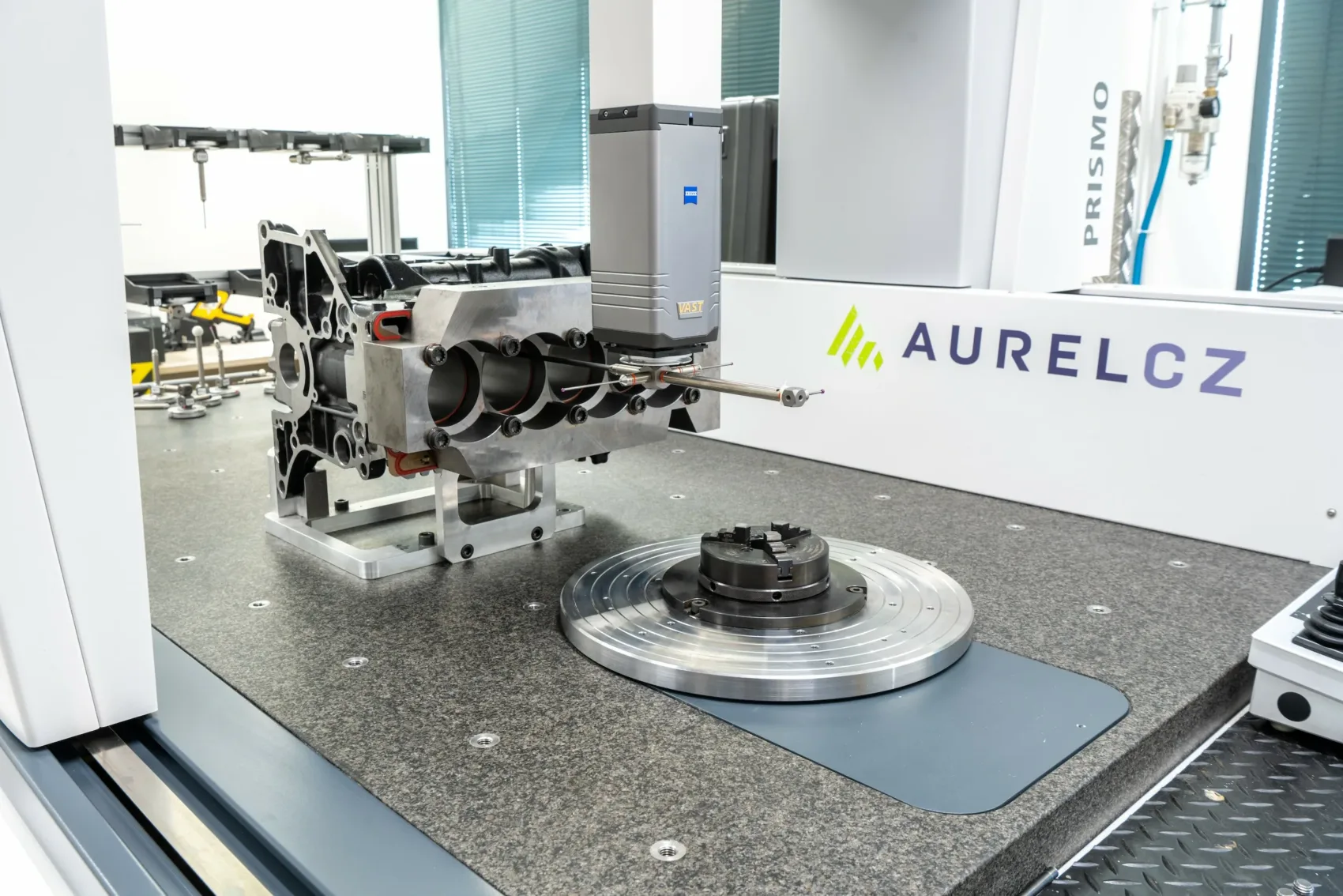
Motorblokk esetén a mérést a gyártási feltételekkel megegyező feltételek mellett végezzük. A blokk „mérőüvegekkel” van felszerelve, hogy megmérje azt az állapotot, amely a megmunkáláskor volt vagy jelen lesz a motorban. A henger belső méretei és kereksége mellett a dugattyúval és a dugattyúgyűrűkkel érintkező területen a főtengely csapágyainak átmérőjét, kerekségét és beállítását vagy a karimák laposságát is mérik. Ezt követi a hengerfelület állapotának ellenőrzése a hónoláshoz. Erre a célra a főüzemben speciális, optikai elven működő mérőberendezéseket alkalmazunk.
Szintén fontos az időbeli mérések statisztikái, amelyek elsősorban az alkatrészek gyártási folyamatának optimalizálására szolgálnak a beszállítók felé. A mért adatokat archiváljuk, hogy összehasonlíthassuk a motorellenőrzés során végzett mérésekkel a motor kopásának objektív értékelése érdekében.
Beszerelés az autóba
Ha az alkatrészek átmennek a minőségügyi osztályon, akkor készen állnak a járműbe való beszerelésre. Motor esetén egy szerelőnek 10 munkanapot vesz igénybe a blokk felszerelése a teljes motorra, és a teljes folyamat a motorműhelyben történik. A motor összeszerelése után a motorfékműhelybe kerül ellenőrzésre, hogy a motor eléri-e a szükséges teljesítményparamétereket. Amikor a motor visszatér, generátorral látják el, majd a sebességváltóval párosítják, majd beépítik a versenyautóba. A teljes autógyártási ütemtervben az ötödik napot a motor és a sebességváltó beszerelésére szánják. A teljes első tengely nagyjából fél nappal az aggregát leállítása és csatlakoztatása után következik.
Mindezek a lépések kulcsfontosságú részét képezik a Škoda versenyautók általános minőségének és tartósságának. A precíz logisztikai láncok, a századmilliméteres pontosság és a gondosan megtervezett építési ütemtervek első pillantásra talán nem látszanak, de ezek jelentik az autó jövőbeni sikerének alapját, és ezzel a gyári csapatban mindenki tisztában van. Erre pedig nap mint nap emlékeztetik őket a versenytrófeákkal teli vitrinek, amelyek közvetlenül az autóépítő boxok mellett helyezkednek el.